1. Paso uno: Fundición
El aluminio se fabrica mediante electrólisis a escala industrial, y las fundiciones de aluminio requieren mucha energía para funcionar eficientemente. Las fundiciones suelen estar ubicadas junto a grandes centrales eléctricas debido a su demanda energética. Cualquier aumento en el coste de la energía, o en la cantidad de energía necesaria para refinar el aluminio a una mayor calidad, incrementa el coste de las bobinas de aluminio. Además, el aluminio disuelto se separa y se transporta a un área de recolección. Esta técnica también implica un consumo energético considerable, lo que también afecta a los precios del mercado del aluminio.
2. Paso dos: laminación en caliente
El laminado en caliente es uno de los métodos más utilizados para adelgazar una placa de aluminio. En este proceso, el metal se calienta por encima del punto de recristalización para deformarlo y darle mayor forma. Posteriormente, este metal pasa por uno o más pares de rodillos. Esto se realiza para reducir el espesor, uniformizarlo y lograr la calidad mecánica deseada. Una bobina de aluminio se crea procesando la lámina a 1700 grados Fahrenheit.
Este método permite producir formas con los parámetros geométricos y las características del material adecuados, manteniendo constante el volumen de metal. Estas operaciones son cruciales para la producción de productos semiacabados y terminados, como placas y láminas. Sin embargo, los productos laminados terminados se diferencian de las bobinas laminadas en frío, que se explicarán más adelante, en que presentan un espesor menos uniforme debido a la presencia de pequeños residuos en la superficie.
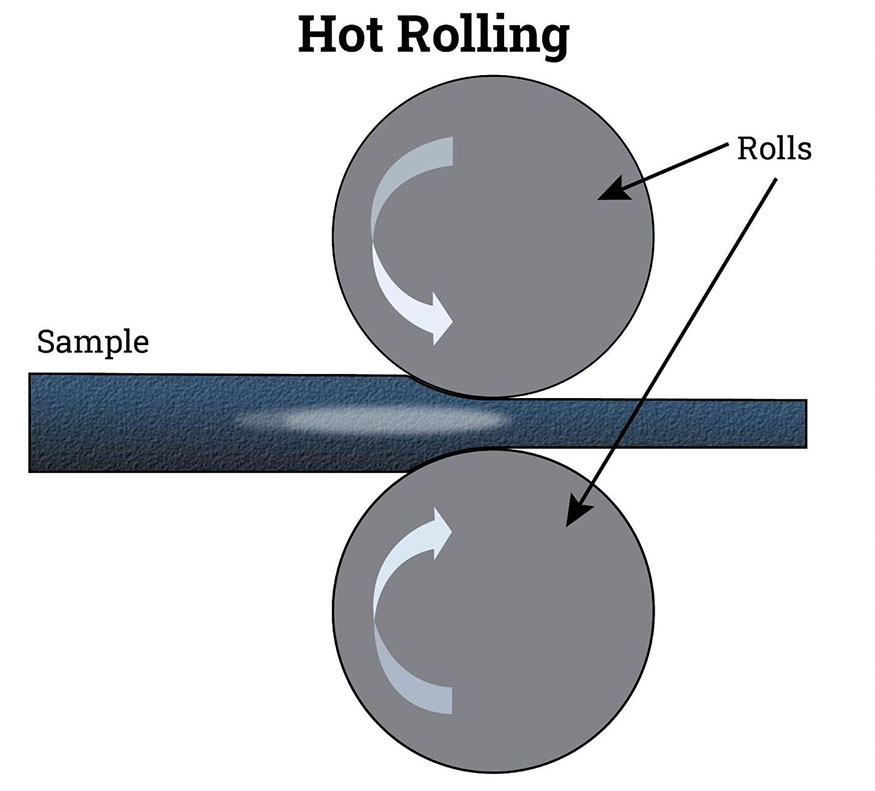
3. Paso tres: laminación en frío
El laminado en frío de flejes metálicos es un área única del sector metalúrgico. El proceso de laminado en frío consiste en pasar el aluminio por rodillos a una temperatura inferior a la de recristalización. La compresión del metal aumenta su límite elástico y dureza. El laminado en frío se produce a la temperatura de endurecimiento por acritud (temperatura inferior a la de recristalización del material), mientras que el laminado en caliente se produce por encima de dicha temperatura. Esta es la diferencia entre el laminado en caliente y el laminado en frío.
Muchas industrias utilizan el procedimiento de tratamiento de metales conocido como laminado en frío para producir flejes y láminas metálicas con el calibre final deseado. Los rodillos se calientan con frecuencia para mejorar la trabajabilidad del aluminio y se utiliza lubricante para evitar que la tira se adhiera a ellos. Para un ajuste preciso, se puede modificar el movimiento y la temperatura de los rodillos. Una tira de aluminio, previamente laminada en caliente y sometida a otros procedimientos, como limpieza y tratamiento, se enfría a temperatura ambiente antes de introducirse en una línea de laminado en frío en la industria del aluminio. El aluminio se limpia enjuagándolo con detergente, lo que endurece la bobina de aluminio para soportar el laminado en frío.
Tras estos pasos preparatorios, las tiras pasan repetidamente por rodillos, perdiendo espesor progresivamente. Los planos reticulares del metal se alteran y desplazan durante el proceso, lo que resulta en un producto final más duro y resistente. El laminado en frío es uno de los métodos más populares para endurecer el aluminio, ya que reduce su espesor al triturarlo y empujarlo a través de los rodillos. Una técnica de laminado en frío puede reducir el espesor de una bobina de aluminio hasta en 0,15 mm.
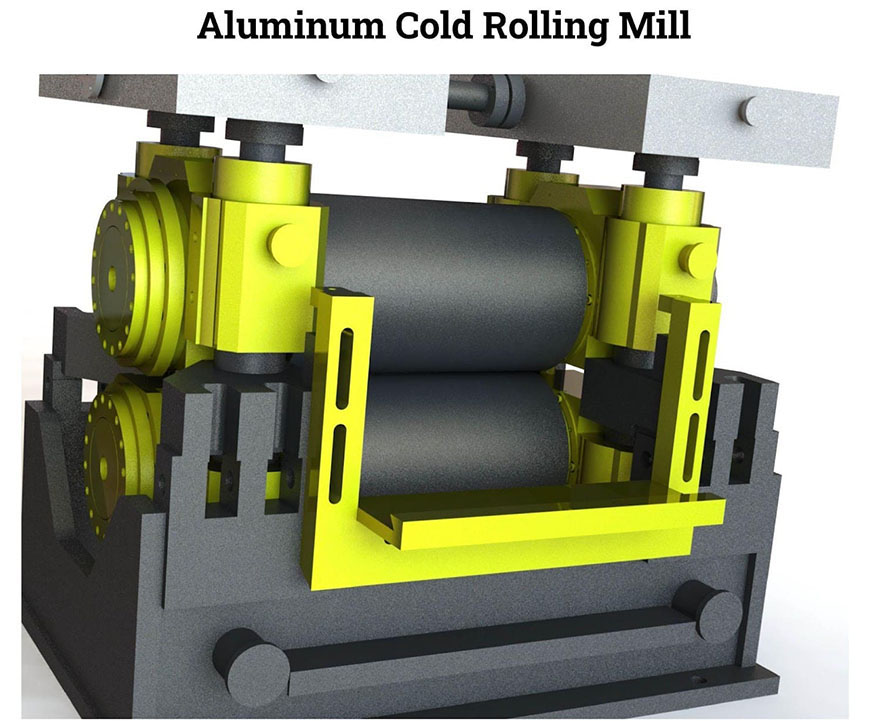
4. Paso cuatro: Recocido
El proceso de recocido es un tratamiento térmico utilizado principalmente para hacer que un material sea más maleable y menos rígido. La disminución de las dislocaciones en la estructura cristalina del material recocido provoca este cambio en la dureza y la flexibilidad. Para evitar la rotura por fragilidad o para que un material sea más manejable para operaciones posteriores, el recocido se realiza con frecuencia después de que el material se haya sometido a un proceso de endurecimiento o trabajo en frío.
Al restablecer eficazmente la estructura cristalina del grano, el recocido restaura los planos de deslizamiento y permite un mayor conformado de la pieza sin aplicar una fuerza excesiva. Una aleación de aluminio endurecida por acritud debe calentarse a una temperatura específica de entre 570 °F y 770 °F durante un período predeterminado, que varía entre treinta minutos y tres horas. El tamaño de la pieza que se recoce y la aleación de la que está hecha determinan la temperatura y el tiempo requeridos, respectivamente.
El recocido también estabiliza las dimensiones de una pieza, elimina los problemas causados por deformaciones internas y reduce las tensiones internas que pueden surgir, en parte, durante procedimientos como el forjado en frío o la fundición. Además, las aleaciones de aluminio que no son tratables térmicamente también pueden recocerse con éxito. Por lo tanto, se aplica con frecuencia a piezas de aluminio fundidas, extruidas o forjadas.
La capacidad de conformado de un material se mejora mediante el recocido. Presionar o doblar materiales duros y frágiles puede ser complicado sin provocar una fractura. El recocido ayuda a eliminar este riesgo. Además, el recocido puede aumentar la maquinabilidad. La fragilidad extrema de un material puede provocar un desgaste excesivo de la herramienta. Mediante el recocido, se puede reducir la dureza del material, lo que a su vez reduce el desgaste de la herramienta. Cualquier tensión residual se elimina mediante el recocido. Por lo general, es mejor reducir las tensiones residuales siempre que sea posible, ya que pueden provocar grietas y otros problemas mecánicos.
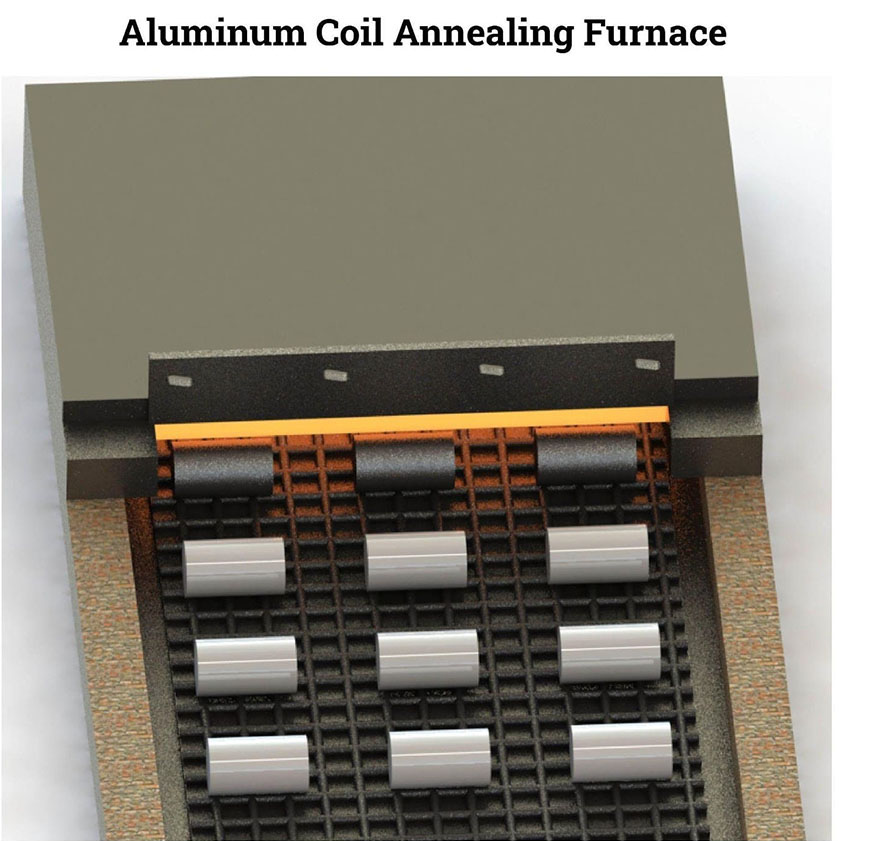
5. Paso cinco: corte y ranurado
Las bobinas de aluminio pueden fabricarse en un rollo continuo muy largo. Sin embargo, para comprimirlas en rollos más pequeños, es necesario cortarlas. Para ello, los rollos de aluminio se pasan por una máquina de corte longitudinal, donde cuchillas extremadamente afiladas realizan cortes precisos. Esta operación requiere mucha fuerza. Las cortadoras cortan el rollo en trozos más pequeños cuando la fuerza aplicada supera la resistencia a la tracción del aluminio.
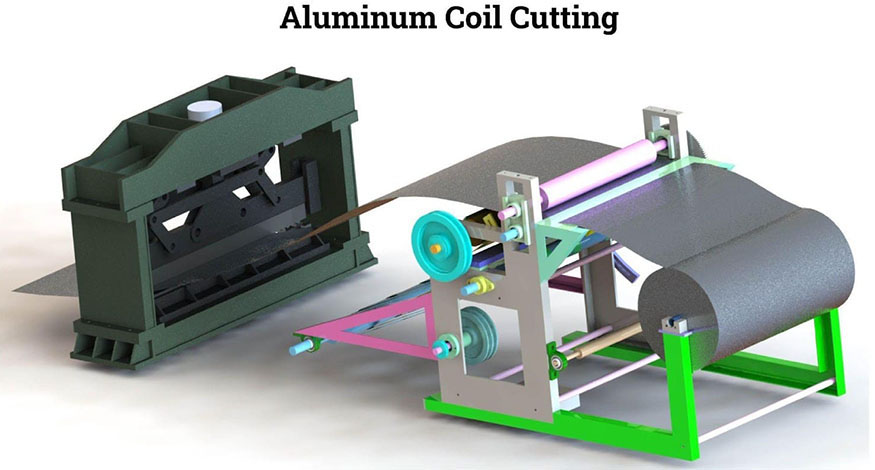
Para iniciar el proceso de corte, el aluminio se coloca en una desenrolladora. Posteriormente, pasa por un conjunto de cuchillas rotativas. Las cuchillas se posicionan para obtener el mejor borde de corte, considerando el ancho y la holgura deseados. Para dirigir el material cortado a la rebobinadora, este se alimenta posteriormente a través de separadores. El aluminio se ata y enrolla para su envío.
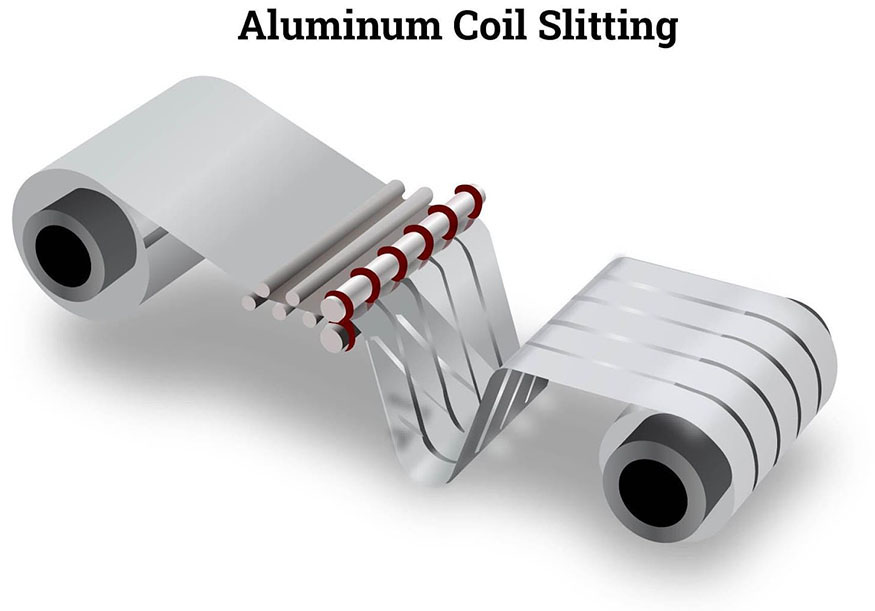
Jindalai Steel Group es la empresa líder en aluminio y proveedora de bobinas, láminas, placas, flejes, tubos y láminas de aluminio. Contamos con clientes en Filipinas, Thane, México, Turquía, Pakistán, Omán, Israel, Egipto, países árabes, Vietnam, Myanmar, India, etc. Envíe su consulta y con gusto le brindaremos asesoramiento profesional.
LÍNEA DIRECTA:+86 18864971774WECHAT: +86 18864971774WHATSAPP:https://wa.me/8618864971774
CORREO ELECTRÓNICO:jindalaisteel@gmail.com sales@jindalaisteelgroup.com SITIO WEB:www.jindalaisteel.com
Fecha de publicación: 19 de diciembre de 2022